Задачи, решаемые системой мониторинга
Мониторинг это последовательный процесс: получение информации о состоянии оцениваемого объекта; передачи информации по каналу связи с перекодированием и преобразованием в новые формы представления; декодирования и анализа переданной информации локальными или системно-аналитическими средствами; использование результатов анализа в системах подготовки принятия решений.
Преобразование исходных данных с технологического оборудования в аналитическую информацию.
Система мониторинга промышленного оборудования (СМПО) - программно-аппаратный комплекс предназначенный для выявления узких мест и потерь в ходе производственного процесса, анализа и сравнения планируемых и фактических показателей производства.
(СМПО)
Относится к системам класса MDC/MDA (Machine Data Collection / Machine Data Acquisition - сбор машинных данных), кроме типовых функций этих систем обладает возможностями многопараметрической экспертной системы и интерактивным взаимодействием с обслуживающим оборудование персоналом.
Основные функции системы:
- 01
Контроль состояния технологического оборудования
- 02
Визуализация метрик производительности;
- 03
Учет и анализ простоев;
- 04
Контроль возникновения простоев;
- 05
Определение реальных норм времени изготовления деталей;
- 06
Расчет ключевых показателей эффективности;
- 07
Учет наработки оборудования;
- 08
Учет времени полезной работы персонала.
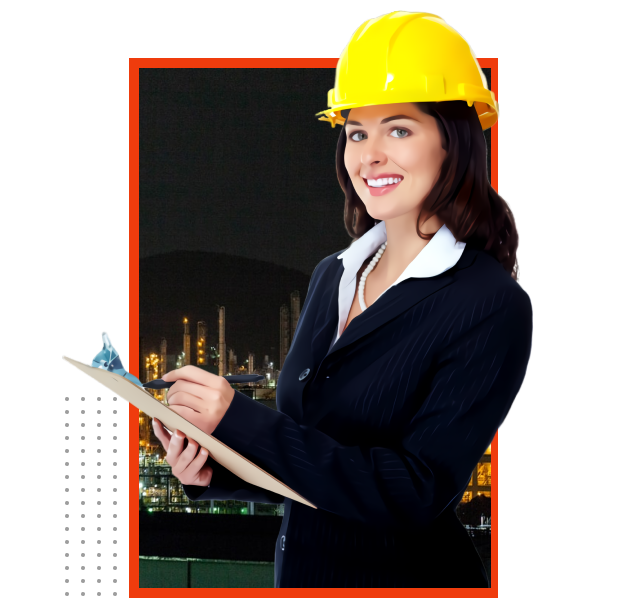
Получите бесплатную консультацию
Оставьте заявку - наш специалист свяжется с Вами и ответит на все вопросы
Основные составляющие системы:
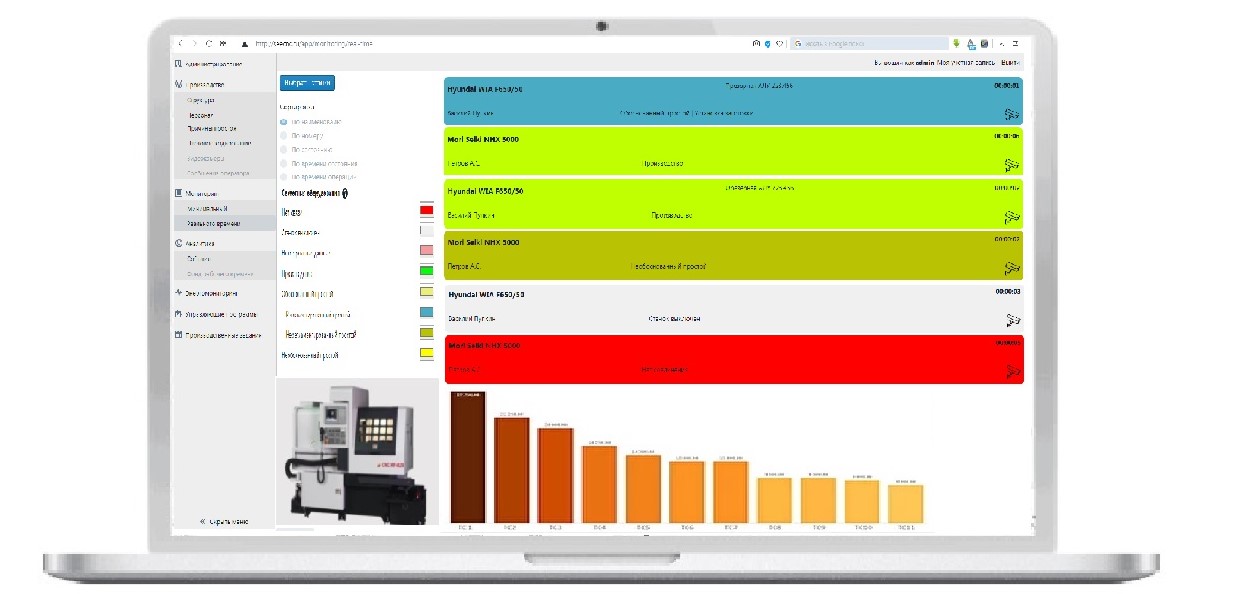
Любые формы отчетов
Подсистема сбора данных на базе электронных блоков мониторинга ForemanPRO и интеллектуальных Industrial Internet of Things, IIoT (Индустриальный или Промышленный Интернет Вещей) датчиков;
Кроссплатформенный программный комплекс информационно-аналитического мониторинга "SeeCNC" (ИАМ "SeeCNC").
Используется проверенное аппаратное решение на базе блоков мониторинга ForemanStandsrd / ForemanPRO и программного обеспечения нового поколения ИАМ "SeeCNC".
Блоки мониторинга серии ForemanPRO проверенное решение для аппаратной основы сбора данных с оборудования. Ранее хорошо зарекомендовали себя при сборе и передачи данных в программный продукт ПТК "Foreman".
Интеграция со специализированными подсистемами вибрационной диагностики оборудования и/или системами защиты оборудования от последствий столкновений, контроля целостности инструмента, подсистемами энергомониторинга и контроля качества электроэнергии. В случае систем защиты от последствий столкновения, можно говорить про частичный функционал SCADA систем.
Автоматизация сбора данных с производственного оборудования открывает возможность более полно использовать его потенциал отслеживая его загрузку, минимизировать непроизводственные простои и своевременно проводить сервисное обслуживание.
Архитектура системы:
Система мониторинга промышленного оборудования (СМПО) представляет собой открытую автоматизированную систему. СМПО имеет модульную структуру, что в случае необходимости позволяет обеспечить поэтапное внедрение системы и расширение без замены программных и аппаратных продуктов и изменений общей структуры системы.
Особенности:
- используется проверенное аппаратное решение на базе блоков мониторинга ForemanPRO/ForemanStandard и программного обеспечения нового поколения ИАМ "SeeCNC".
Аппаратные средства
Многофункциональные электронные блоки мониторинга серии Foreman служат для первичной обработки данных полученных с оборудования, их
нормализации. Идентификации и интерактивного взаимодействия с обслуживающим персоналом. Уточнения причин временных потерь и получения
информации о номенклатуре обрабатываемой продукции.
Выпускается унифицированная линейка многофункциональных электронных блоков мониторинга ForemanStandard и ForemanPRO. С модельным рядом и функционалом можно ознакомиться на специализированном сайте.
Программные средства
Кроссплатформенное программное приложение, с широкими возможностями масштабирования, позволяет гибко и единообразно интегрировать в информационную инфраструктуру предприятия данные полученные от различных источников, в том числе и от специализированных блоков мониторинга, которые в свою очередь собирают их с технических средств производства, таких как:
- Универсальные станки
- Обрабатывающие центры
- Гальванические линии
- Станки с ЧПУ
- Производственные линии
- Печи отжига
и другое разнообразное промышленное оборудование, как например швейное оборудование, оборудование производства пластиковых изделий и т.п.
- Визуализация
- Аналитика
- Алгоритмы
- Вычисления, нормализация
- Исходные данные
- Источники данных
- Визуализация – отображение информации в удобном для восприятия виде с целью выявления и устранения проблем.
- Аналитика, позволяет системе генерировать новые данные из ранее собранной информации. Выявление закономерностей, возможных негативные причины, основных проблем.
- Алгоритмы, позволяющие получить информацию в удобном виде для дальнейшего анализа.
- Вычисления, нормализация - первичная обработка "сырых данных" полученных с оборудования.
- Исходные данные в режиме истории и данные в реальном времени, соответствующим образом структурированные, проиндексированные и нормализованные.
- Персонал
- Оборудование
- Внешние
данные - Работы,
фонд времени
- Источники данных. Все те данные, что пытаются использовать сейчас в ручном режиме: события простоев, журналы работ, наряды, сменно-суточные задания и т. д. Все эти данные в автоматическом и автоматизированном виде собираются системой.
Собранная с технологического оборудования информация имеет возможность дополнительно актуализироваться в контексте рабочих заданий, рабочих операций и идентификаторов деталей, чтобы в дальнейшем создавать требуемые отчеты или передавать данные в смежные информационные системы. Обеспечивается контроль простоев с детализацией их причин, в результате формируется массив статистических данных с оценкой длительности каждого конкретного простоя или их суммарных значений. Полученная информация дает возможность проведение коррекции производственных планов и пересмотра сменно-суточных заданий. При наличии информации по планируемому выпуску продукции можно проводить сравнение плана с фактом, без существенных трудозатрат. Система ведет учёт общей наработки оборудования, эта информация при экспорте ее в смежные системы, позволяет оперативно проводить ППР и заранее просчитать его влияние на выполнение плана производственной программы.
Прикладное программное обеспечение для визуализации данных.выполнено как веб-сервис, что позволяет в случае необходимости получать нужную информацию в простой и доступной форме. Продукт реализован как микросервисная архитектура, доступно открытое API для интеграции со сторонними IT системами.
- Полученные результаты могут удивить даже самых опытных специалистов, которые считают, что знают свое производство досконально. Программное обеспечение ИАМ SeeCNC покажет истинную картину без домыслов и догадок о самых незначительных деталях производственного процесса. Только такой подход позволяет держать ситуацию на производстве под контролем.